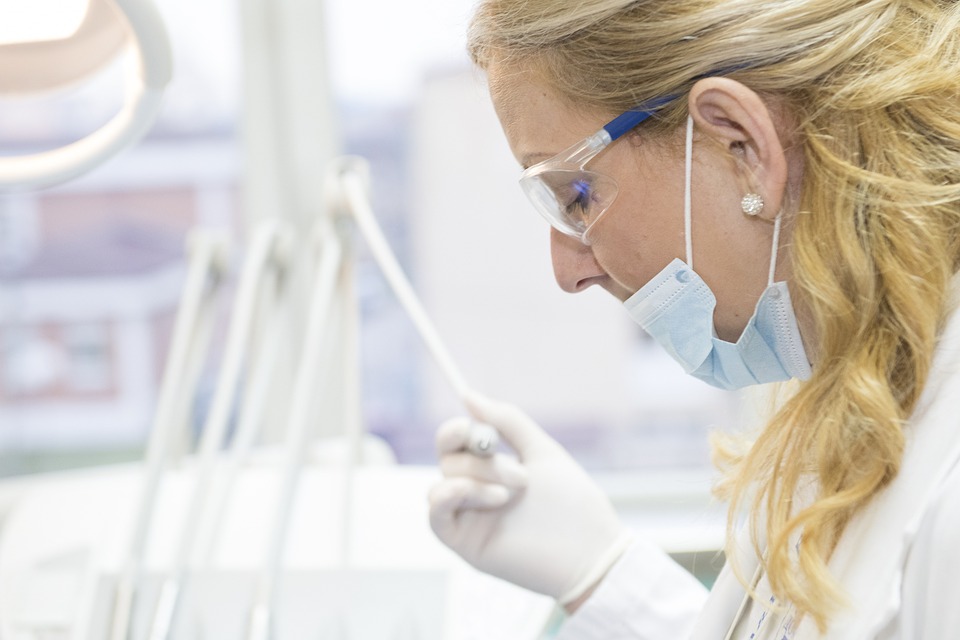
Faster production means shorter lead times and ultimately more economic benefits for the manufacturer. The overall advantages of Rapid Prototyping seem limitless.
The trial-and-error approach is an integral part of the MedTech industry and prototyping is the best way to do that. Quickly checking different iterations of the design and testing which one is the best in fulfilling all the health/safety requirements while meeting the costs and design parameters is difficult. In many cases, investors also demand seeing the product in actual performance before releasing the funds, and going through all that red tape traditionally means a slower market penetration rate and a loss in opportunity costs along with existing market share.
Rapid Prototyping can avoid all that if applied properly. It is the quick development of a product that can be used to test out the functionality before a final production runs for the market. Businesses use prototypes to learn more about the performance of the product, gain valuable feedback, optimize the design, and finally start large-scale manufacturing.
For the medical sector, prototyping is a viable way for manufacturers to keep up with the dynamic demands of the industry and continuously optimize the existing designs through innovation. It is also how smaller companies quickly react to the demand in the market and accelerate their production process to gain market share from the larger players.
Another reason why rapid prototyping is so important for the medical sector is the involvement of healthcare professionals. Since they are not product designers, they are unaware of the intricacies of the designing and manufacturing process. However, they are experts at using MedTech devices for the betterment of their patients. With rapid prototyping, businesses can incorporate the valuable feedback of medical professionals, address the imperfections in the designs, and finally send the right product for mass manufacturing.
Rapid Injection Molding and the Medical Industry
With the progression of time, advanced engineering materials continue to enter the mainstream market to fulfill the requirements of the industry. Thermoplastics and silicon materials, for example, have hundreds of variations that are bio-compatible, chemically stable, and versatile enough to meet the changing demands of the medical industry. Moreover, thermoplastics are cost-effective as well, which makes business sense to use them for production.
When it comes to the mass production of thermoplastic products, plastic injection molding is one of the most popular and viable methods that deliver the perfect combination of quality, consistency, and speed. Injection molding pressurizes molten plastics into a pre-determined mold to create a product of the same form. The process is an excellent choice as it has specific tolerance and even achieves economies of scale as production increases.
Rapid injection molding is a similar concept but focuses more on speed than longevity to quickly deliver cost-effective prototypes. A significant portion of the overall lead time for injection molding projects goes into the creation of the mold. Reducing that time delivers a quick batch ready for demonstrations and experiments.
However, the enhanced speed of rapid injection molding comes at a cost. The molds are not too durable and can’t handle long production runs. That is ideal because prototypes generally go through many design iterations and creating expensive and durable molds would only add to the losses for the business.
Leo Huang, the CEO of a global manufacturing business name RapidDirect based in China, believes that rapid injection molding is perfect for businesses.
“Rapid injection molding acts as a bridge between design and production phases where it minimizes risks and improves product validation well before investing the time and resources into mass manufacturing”
That is exactly the case. A low-cost mold with a small production run that points out the flaws of the product before mass manufacturing can save the device manufacturer a lot of hassle down the line. This is especially true for medical applications where even the smallest deviation or flaw can have a lot of consequences down the line.
Having a small batch tested out by doctors and other healthcare professionals can save the manufacturers from a lot of liability. There is a gap between product designers and medical professionals and it might become problematic for complicated devices with a plethora of intricate features.
Rapid injection molding bridges that gap to ensure both functionality and cost-effectiveness at the fastest speed. Quicker turnaround times mean that the product gets available in the market at the quickest time, thereby increasing the business’ market share because of the first mover’s advantage.
Key Takeaways
Medtech products and devices come with additional requirements because of what’s at stake. People’s lives and health. However, businesses also have to care about competition, economics, and business shares to take all the right decisions. Rapid injection molding is an excellent method that allows businesses to incorporate valuable feedback from medical practitioners and take the right product free from any flaws to the market in the shortest time.